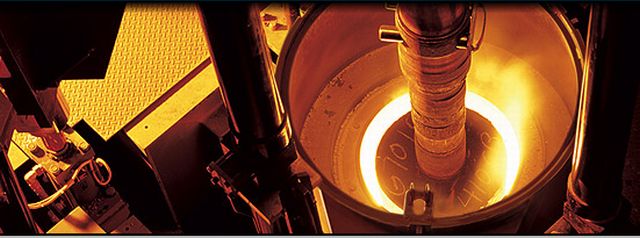
Die Casting and Finding a Die Casting Manufacturer
Die casting is a process in which molten metal is poured into a mold cavity, and the metal hardens in the shape of the mold. Die casting uses alloys which can be made of various metals, like zinc, lead, tin, magnesium, pewter, and copper.
Die casting often involves the use of high pressure. This is how metal alloy casting is done for about 50% of all production. A second method involves low pressure, although this only works for certain items, and with its overall usefulness increasing in the last few years. Gravity die casting, vacuum die casting, and squeeze die casting are three other methods that are also used but not very often.
Aluminum, even with its thinness, is a popular alloy for die casting, mainly because it is lightweight and stable, as well as resistant and mechanically excellent. Since aluminum remains strong in high temperatures and can conduct both heat and electricity, most manufacturers of high end products consider it the alloy of choice. In aluminum casting, the mold is sometimes not removed even after the alloy has hardened and taken its shape. This is because the mold can also provide external protection for the alloy. Aluminum is usually subjected to the cold chamber process because it has a high melting point.
If you are looking for an alloy steel casting manufacturer that you can partner with in business, you have to look a little more closely in to your prospects. First, find a manufacturer who knows how to tweak the production process to achieve specific goals with a part or product. With the die casting process being very expensive, a company can only save on the high manufacturing cost by producing large volumes. However, with the right manufacturer as your partner, you can sit down and rework everything so you can come up with a new and better solution that creates the same intended product.
Also note that a good super duplex casting manufacturer uses an efficient approach in defining what's best for the company and its requirements for production. They always know what processes and materials are the best to use for their products. They also know how to tailor their services according to the satisfaction of their customers, and they can find ways to satisfy these customers without making they pay so much. They will list down packages, prices, and other details and this lets them view their options, compare, and choose those which are to the best benefit of their production processes.
Finally, with an experienced die casting manufacturer, time is always of the essence, and is viewed as crucial in terms of how successful a product is based on when it is released and its availability. They are aware of how much time they have and will never put it to waste. Even when unavoidable events or accidents occur, they will always have a backup plan of action so that the production process continues and product quality is never compromised.